Medium frequency induction furnace technology development promotion, metal heat processing field of increasing demand; medium frequency furnace operation process through the use of electromagnetic induction principle, compared with the traditional coal-fired furnace more energy-saving, environmental protection. Medium frequency furnace in the later use process, need to do a good job of basic maintenance and management, to avoid the equipment can not start normally, have abnormal sound, thyristor burned and other phenomena.
(1) Check and clean the radiator to maintain efficient cooling effect, acid cleaning if necessary
(2) Check whether the water cooling system is blocked and leaking, whether the water pressure relay is sensitive, and the temperature difference of the inlet water should not be greater than 35℃ in general. IF power supply, induction coil, water cable, etc. need water for cooling, so water is vital for furnace equipment. The chance of damage to the furnace equipment due to cooling water failure is higher. Because most of the devices being cooled are charged bodies, such as thyristors, induction coils, water cables, etc., the conductivity of the cooling water used to directly cool these devices must be lower than the specified value, and the connecting hose must be a carbon-free rubber hose. In addition, the cooling water inlet temperature, outlet temperature, water pressure and flow rate must be in line with the design provisions. The cooling water system of the electric furnace is equipped with various sensors to monitor the relevant parameters of the cooling water. When the cooling water parameters are abnormal and exceed the set value, an alarm is raised or the operation of the equipment is stopped.
Fire resistant casing, also known as high temperature resistant casing, silicone rubber fiberglass casing, is made of high purity alkali-free glass fiber compiled into a tube, and then coated with organic silicone on the outer wall of the tube by vulcanization treatment. After vulcanization, it can be used for a long time in the temperature range of -65°C to 260°C and maintain its soft and elastic properties.
Fire-resistant sleeves can be used in high-temperature workshops, where the internal temperature of many pipes, valves or equipment is very high, and if they are not covered with protective materials, they can easily cause burns or heat loss to personnel. Fire-resistant casing has better thermal stability than other polymer materials as well as irradiation resistance and heat insulation to prevent accidents and reduce energy consumption, and also prevent the heat of the medium inside the pipe from being directly transferred to the surrounding environment and making the temperature of the workshop too high, saving cooling costs. Moisture-proof, oil-proof, climate-proof aging, anti-pollution, and prolong the service life of equipment.
The cables and hydraulic pipes near the smoke barrier arm of the medium frequency induction furnace are easily damaged due to high temperature steel spattering. Hebei Zeal refractory sleeve can effectively protect the hydraulic tube and cable from high temperature, and is an economical high temperature protection solution to protect the hose and cable at the steel splash.
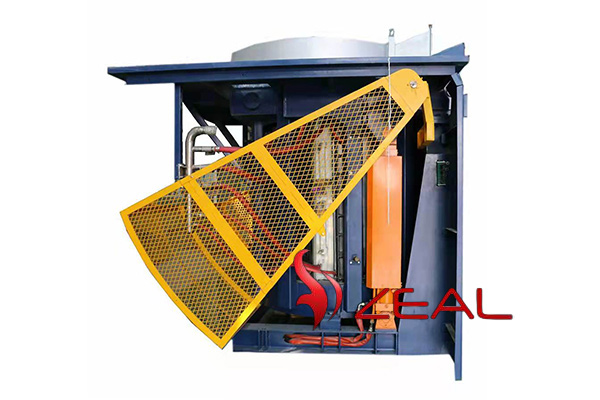